The Best Strategy To Use For Premier Aluminum Llc
The Best Strategy To Use For Premier Aluminum Llc
Blog Article
The 9-Minute Rule for Premier Aluminum Llc
Table of ContentsPremier Aluminum Llc - An OverviewThe smart Trick of Premier Aluminum Llc That Nobody is DiscussingRumored Buzz on Premier Aluminum LlcSome Ideas on Premier Aluminum Llc You Should Know
(https://leetcode.com/u/premieraluminum/)Typically, a buyer's main duty was to locate certified and receptive providers. In many cases, purchasers presumed that any type of distributor going to contractually fulfill the acquisition need was certified. Using reduced cost and unqualified distributors can trigger high quality issues, and squandered time and cash in the lengthy run. To aid you with the process, here are some points to consider when selecting the ideal metal spreading distributor.
For instance, a company that only makes use of the financial investment casting process will certainly attempt to offer you on why that procedure is best for your application. But suppose making use of the sand spreading procedure is best for you and your needs? Rather, seek a distributor that uses a range of casting procedures so the most effective option for YOU is chosen
If collaborating with a single source for every one of your spreading requires is crucial to you, the supplier requires to be diverse in its capabilities. When combined with various other integrated capabilities, this can help streamline and compress the supply base. When picking the right spreading distributor, careful factor to consider ought to be given to top quality, service, and rate.

Premier Aluminum Llc Things To Know Before You Buy
Purchasers increasingly select casting providers that have machining capabilities. If the spreading supplier discovers an issue during machining, the issue is settled faster with no dispute over whose fault it is.
What do you need from your casting vendor? Are you looking for a person to just deliver a metal element to your front door or do you require a lot more?
Some foundries are minimal or specialized. Make sure the supplier can fulfill all your material or alloy demands to remove the requirement for multiple vendors.
Some Of Premier Aluminum Llc
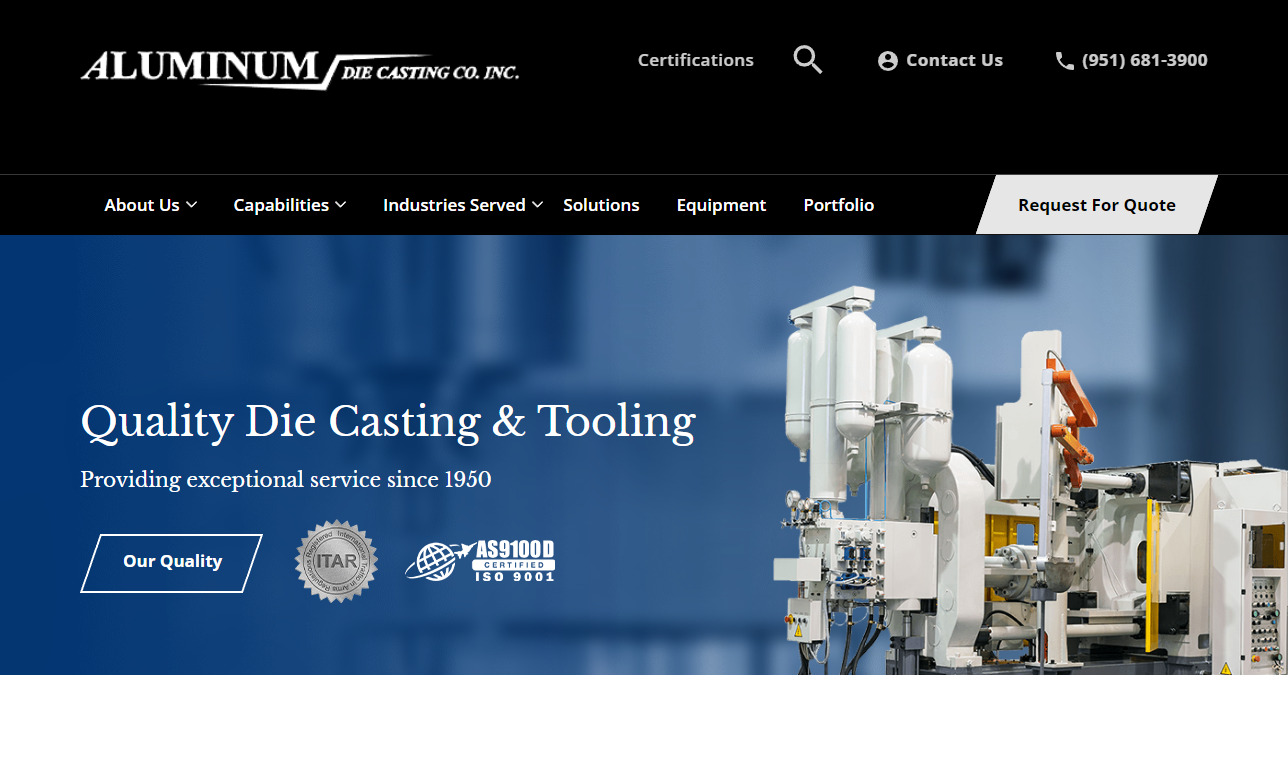
Research the vendor's website. Speak with a sales associate or service affiliate. Ask a great deal of inquiries. See their center. Get an understanding of what they can do for you and if you can see yourself developing a strong, shared connection with them.
Aluminum is also lightweight and has excellent rust resistance, making it suitable for applications where weight and toughness are vital factors. Additionally, light weight aluminum spreading is a cost-efficient approach of manufacturing, as it needs less power and sources than various other techniques. Iron casting, on the various other hand, includes putting molten iron into a mold and mildew to develop a wanted shape.
3 Simple Techniques For Premier Aluminum Llc
Iron spreading is also able to hold up against high temperatures, making it suitable for use in applications such as engine parts and industrial equipment. However, iron spreading can be much more expensive than aluminum casting because of the greater cost of resources and the power required to thaw the iron. When choosing between aluminum spreading and iron spreading, it is very important to think about the certain needs of the application.
If strength and durability are more vital, iron spreading might be the better choice. Various other factors to take into consideration include expense, production quantity, and preparation. Finally, both aluminum casting and iron spreading have their very own distinct benefits and disadvantages. By very carefully considering the specific requirements of the application, makers can select the most effective process why not find out more for their product.ZheJiang Dongrun Casting Sector Co,. Ltd was constructed in 1995, We have actually remained in the casting sector for even more than 25 years. Die casting is the name offered to the
process of developing intricate metal parts via use of mold and mildews of the component, also understood as passes away. The process utilizes non-ferrous steels which do not contain iron, such as aluminum, zinc and magnesium, due to the desirable homes of the steels such as reduced weight, higher conductivity, non-magnetic conductivity and resistance to rust. Die casting production is fast, making high manufacturing degrees of parts easy.
It generates even more components than any type of various other procedure, with a high degree of accuracy and repeatability. To find out more regarding die casting and die casting materials utilized at the same time, continued reading. There are 3 sub-processes that fall under the group of die casting: gravity die spreading (or permanent mold casting), low-pressure die spreading and high-pressure die spreading. The pure steel, also referred to as ingot, is included to the heating system and kept at the molten temperature level of the metal, which is after that transferredto the shot chamber and injected into the die. The pressure is then kept as the steel solidifies. Once the metal strengthens, the cooling procedure starts. The thicker the wall of the component, the longer the cooling time because of the quantity of indoor metalthat also needs to cool down. After the part is completely cooled down, the die cuts in half open and an ejection system pushes the element out. Adhering to the ejection, the die is shut for the next shot cycle. The flash is the additional product that is cast during the procedure. This must be trimmed off utilizing a trim tool to
leave simply the primary element. Deburring eliminates the smaller sized pieces, called burrs, after the trimming procedure. The element is polished, or burnished, to give it a smooth finish. Nevertheless, this proved to be an unreliable test, since the tester could cut into a piece and miss an area with porosity. Today, leading producers utilize x-ray testing to see the entire interior of parts without cutting into them. This allows them to a lot more precisely accept or turn down parts. To reach the ended up product, there are three primary alloys made use of as die casting product to select from: zinc, light weight aluminum and magnesium. Zinc is just one of the most used alloys for die spreading as a result of its reduced expense of raw materials. Report this page